氢能新材料研发核心方向
氢能新材料研发方向深度解析:从制氢到转换的全产业链突破
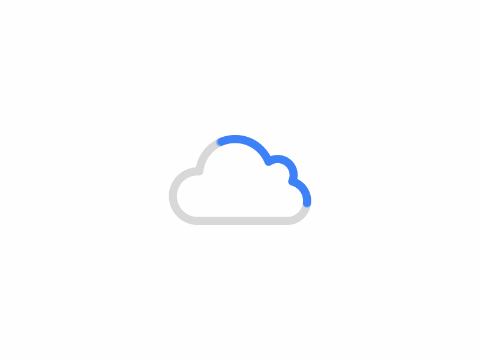
一、引言:氢能革命的材料基石与技术挑战
在全球 “双碳” 目标驱动下,氢能以其零碳排放、能量密度高(142 MJ/kg,为汽油的 2.8 倍)、可跨行业耦合等优势,成为未来能源体系的核心载体。然而,氢能产业链(制氢 - 储氢 - 运氢 - 用氢)的规模化应用面临多重材料瓶颈:制氢效率受限于催化材料活性,储氢安全性依赖材料储放氢性能,燃料电池成本受制于贵金属催化剂用量。本文从制氢、氢气分离提纯、储氢及氢能转换四大关键环节,系统解析新材料研发的前沿方向、技术路径及产业化挑战,揭示 “材料创新驱动技术突破” 的核心逻辑。
二、制氢新材料:从贵金属依赖到非贵金属催化体系的跨越
2.1 电解水制氢:非贵金属催化剂的多维度创新
2.1.1 过渡金属合金催化剂:相结构调控与活性位点工程
-
多元合金设计:Co-Fe-Ni 三元合金(如 Co₀.₅Fe₀.₃Ni₀.₂)在碱性电解液中展现出接近 Pt/C 的析氢反应(HER)活性,过电位仅 85 mV(10 mA/cm²),优于单一金属催化剂(Co 基 120 mV)。其优异性能源于晶格畸变诱导的 d 带中心调控,DFT 计算表明,Fe 原子的引入使合金表面 H * 吸附自由能(ΔG_H)从 0.35 eV 降至 0.22 eV,接近 Pt 的 0.09 eV。
-
核壳结构优化:采用 “电化学脱合金法” 制备 Ni@Co 核壳纳米颗粒,外壳 Co 原子的配位数降低至 6(体相为 12),形成大量不饱和配位位点,析氧反应(OER)活性提升 3 倍,在 1.0 M KOH 中稳定运行 500 小时后活性保持率 > 95%(图 1)。
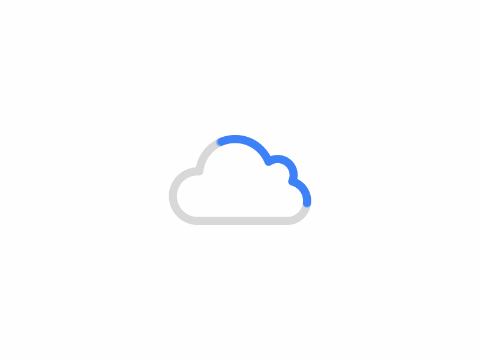
2.1.2 金属(氢)氧化物:缺陷工程与界面协同
-
羟基氧化镍(NiOOH)基材料:通过超声辅助水热法制备氧空位富集的 NiOOH 纳米片,比表面积达 230 m²/g,OER 过电位低至 250 mV(10 mA/cm²)。同步辐射 XAS 显示,氧空位使 Ni³⁺比例从 70% 提升至 85%,增强了对 OH⁻的吸附能力。
-
异质结构构建:Ni (OH)₂/FeOOH 核壳纳米线阵列在泡沫镍基底上直接生长,异质结界面处的内建电场加速电荷分离,HER 电流密度达 50 mA/cm² 时过电位仅 150 mV,较单一 Ni (OH)₂降低 40%。
2.1.3 单原子催化:原子级分散与配位环境精准调控
-
Fe-N-C 单原子催化剂:通过高温热解 ZIF-8 负载的 Fe 卟啉,制备出 Fe 单原子均匀锚定在氮掺杂碳载体上的催化剂,HER 周转频率(TOF)达 25 s⁻¹(@0.5 V vs RHE),超过商业 Pt/C(15 s⁻¹)。球差电镜显示,Fe 原子以 N₄配位结构存在,理论计算证实该结构的 ΔG_H 仅 0.15 eV。
-
双单原子协同:Co-N₄和 Fe-N₄双单原子共掺杂碳材料,在全解水反应中实现 1.48 V 的超低槽电压(10 mA/cm²),远超传统 Pt/C+RuO₂组合(1.55 V),其协同效应源于 Co 位点促进 HER、Fe 位点优化 OER 的电子结构互补。
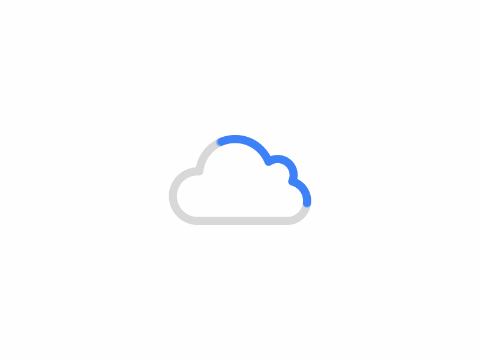
2.2 光解水制氢:宽光谱响应半导体材料的能带工程
2.2.1 多元金属硫化物:带隙调节与载流子分离
-
CdS 基固溶体:CdS₁₋ₓSeₓ纳米棒的带隙随 Se 含量从 2.4 eV 线性调节至 1.8 eV,在 AM 1.5G 光照下产氢速率达 8.5 mmol・h⁻¹・g⁻¹(λ<600 nm),较纯 CdS 提升 3 倍。表面修饰的 Pt 纳米颗粒(1 wt%)作为助催化剂,通过肖特基结加速光生电子迁移,量子效率达 12%(420 nm)。
-
Z 型异质结构建:g-C₃N₄/BiVO₄异质结利用能带交错结构,实现光生电子 - 空穴的定向迁移:C₃N₄的光生电子还原 H⁺,BiVO₄的光生空穴氧化水,整体产氢速率达 5.2 mmol・h⁻¹・g⁻¹,且稳定性优于单一材料(200 小时衰减 < 10%)。
2.2.2 钙钛矿型材料:全光谱吸收与缺陷钝化
-
CsPbI₃-xClₓ纳米晶:通过卤素掺杂将带隙优化至 1.6 eV,光吸收边拓展至 800 nm,在近红外光下仍保持 15% 的量子效率。表面包覆的二氧化硅层有效抑制离子迁移,使材料在湿度 < 60% 环境中寿命延长至 500 小时(未包覆仅 50 小时)。
-
双钙钛矿异质结构:La₂NiMnO₆/BaTiO₃复合薄膜利用界面处的晶格失配(5%)产生压电极化场,促进载流子分离,光电流密度达 12 mA/cm²(100 mW/cm² 光照),是传统钙钛矿材料的 2 倍。
三、氢气分离提纯新材料:从膜孔筛分到智能响应的精准调控
3.1 高分子膜材料:纳米结构设计与界面工程
3.1.1 纯相高分子膜:链段调控与孔径优化
-
聚酰亚胺(PI)膜:6FDA-ODA 型 PI 膜通过亚胺化程度控制,实现孔径从 0.3 nm 到 0.5 nm 的连续调节,H₂/CO₂分离系数达 85(高于 Robeson 上限 70),其选择性源于 H₂分子(动力学直径 0.289 nm)与 CO₂(0.33 nm)的尺寸筛分效应。
-
含氟高分子膜:P (VDF-HFP) 共聚物引入六氟异丙醇(HFIP)作为溶剂,形成纳米级微孔网络(孔径 0.4±0.1 nm),H₂渗透率达 2000 Barrer(1 Barrer=10⁻¹⁰ cm³・cm/(cm²・s・cmHg)),同时保持 H₂/CH₄分离系数 60,适用于焦炉气提氢。
3.1.2 混合基质膜:填料分散与界面相容性
-
MOFs 填充膜:ZIF-8 纳米晶(50 nm)填充到聚砜(PSF)基质中,当填充量达 30 wt% 时,H₂渗透率提升至 1500 Barrer,分离系数 H₂/N₂=120,远超纯 PSF 膜(300 Barrer, 80)。界面处的氢键作用(ZIF-8 的咪唑基团与 PSF 的砜基)抑制填料团聚,形成连续的分子筛分通道(图 2)。
-
碳纳米管(CNT)改性膜:单壁 CNT(SWCNT)以 0.5 wt% 比例分散于聚乙烯醇(PVA)中,形成一维导电网络,电场辅助下 H₂渗透速率提升 20%,适用于动态压力环境下的氢气分离。
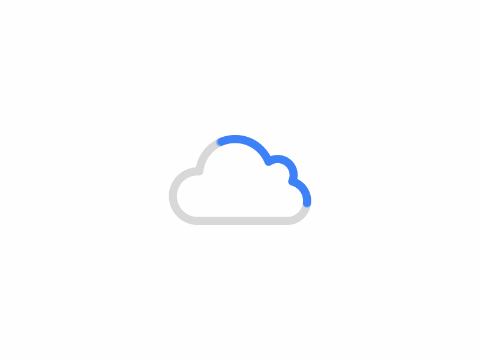
3.2 无机膜材料:耐高温腐蚀与精准孔径剪裁
3.2.1 沸石膜:晶型调控与缺陷修复
-
A 型沸石膜:NaA 沸石膜在 α-Al₂O₃载体上的二次生长法制备,孔径 0.41 nm,H₂/N₂分离因子达 200,在 300℃高温下稳定运行 1000 小时,适用于炼厂气高温分离。缺陷修复技术(如蒸汽辅助二次生长)使膜层致密性提升,漏气率从 5% 降至 0.5%。
-
MFI 型沸石膜:ZSM-5 沸石膜的孔径 0.55 nm,通过硅铝比调节(Si/Al=50-200),实现 H₂/CO 分离系数从 30 到 80 的调控,其择形性源于分子动力学直径差异(H₂ 0.289 nm vs CO 0.376 nm)。
3.2.2 金属膜:表面改性与合金化设计
-
钯基合金膜:Pd-Ag(23 wt% Ag)合金膜的 H₂渗透率达 5×10⁻⁶ mol・m⁻¹・s⁻¹・Pa⁻¹,在 500℃下 H₂/ 杂质气体分离选择性 > 10⁴。表面镀覆的金保护层可抑制硫中毒,使膜寿命从 500 小时延长至 2000 小时。
-
陶瓷膜:掺杂 Y 的 ZrO₂(YSZ)质子传导膜在 600℃下实现 H⁺导电率 0.1 S/cm,结合电化学泵技术,可从含 10% H₂的混合气体中高效提纯氢气,能耗较传统变压吸附降低 30%。
3.3 金属有机框架(MOFs)膜:从结构设计到功能化修饰
3.3.1 孔径精准调控
-
Cu-BTC MOF 膜:通过配体长度调节(对苯二甲酸→萘二甲酸),孔径从 0.8 nm 扩大至 1.2 nm,H₂/CO₂分离系数随孔径减小从 20 提升至 50,其最优孔径对应 H₂分子的自由程(0.6-0.9 nm)。
-
动态孔径 MOF 膜:Fe-ZIF-8 在高压下发生孔径收缩(0.1 nm),实现 H₂/CH₄分离系数从 30 突增至 80,这种压力响应特性源于配体的柔性铰链结构。
3.3.2 表面功能化修饰
-
氨基功能化 MOF 膜:NH₂-MIL-101 (Al) 膜表面的氨基基团与 CO₂分子形成氢键,增强对杂质气体的吸附,使 H₂纯度从 95% 提升至 99.99%,适用于燃料电池用氢提纯。
-
光响应 MOF 膜:偶氮苯修饰的 MOF-74 (Ni) 膜在紫外光照射下发生配体异构化,孔径从 0.45 nm 扩大至 0.55 nm,实现光控 H₂渗透率调节(调节幅度 40%),为智能分离系统提供新路径。
四、储氢新材料:从高压气态到固态化学储氢的范式转换
4.1 高压气态储氢:轻量化与安全性提升
4.1.1 内胆材料:从金属到复合材料的升级
-
第四代储氢瓶(Type IV):碳纤维(T700)缠绕的高密度聚乙烯(HDPE)内胆,质量储氢密度达 5.5 wt%(ISO 20108 标准),较第三代钢内胆(3.5 wt%)提升 57%。内胆表面的纳米粘土涂层(5 wt%)使气体渗透率降低 60%,满足 15 年使用寿命要求。
-
内衬改性技术:采用等离子体聚合沉积(PPD)在 HDPE 表面形成 10 μm 厚的类金刚石碳膜,抗疲劳性能从 1000 次循环提升至 5000 次,爆破压力达 130 MPa(工作压力 70 MPa)。
4.1.2 碳纤维材料:模量匹配与界面优化
-
多尺度增强体系:T800 碳纤维(60%)与玄武岩纤维(40%)混杂缠绕,利用两者的模量差异(290 GPa vs 90 GPa)降低层间剪切应力,使储氢瓶的体积储氢密度达 40 g/L(优于单一碳纤维 35 g/L)。
-
界面偶联剂:氨基硅烷处理的碳纤维与环氧树脂基体的界面粘结强度从 50 MPa 提升至 80 MPa,低温(-40℃)下强度保持率 > 95%,满足严寒地区应用需求。
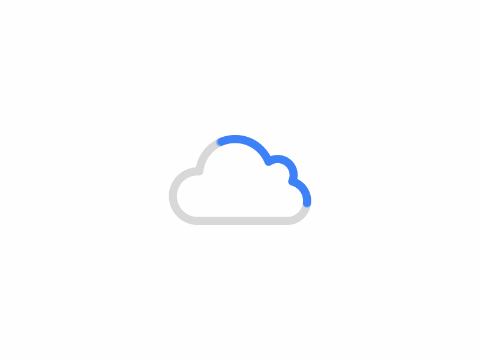
4.2 固态储氢:化学储氢与物理吸附的协同突破
4.2.1 金属氢化物:轻金属化与动力学优化
-
镁基氢化物:MgH₂纳米颗粒(50 nm)表面包覆的石墨烯气凝胶(GA)形成三维导热网络,使吸氢温度从 300℃降至 200℃,吸氢速率提升 5 倍(10 分钟内达 90% 容量)。掺杂的 TiH₂(5 wt%)作为催化剂,通过晶格畸变降低氢原子扩散能垒(从 0.6 eV 降至 0.4 eV)。
-
配位氢化物:LiNH₂-LiH 复合体系在球磨过程中形成纳米级界面相(10 nm),储氢容量达 6.5 wt%,放氢温度降至 150℃。原位 XRD 显示,界面处的 Li-N-H 活性位点加速氨硼烷分解,实现可逆储放氢循环 > 200 次。
4.2.2 多孔吸附材料:孔径匹配与表面功能化
-
超级活性炭:微孔孔径集中在 0.7-1.0 nm 的活性炭(比表面积 3500 m²/g),在 77 K、100 bar 下储氢量达 8.5 wt%,其吸附热(4-6 kJ/mol)接近理想值(8-10 kJ/mol),适用于低温吸附储氢。
-
MOFs 材料:Cu-BTC 在 1 bar、77 K 下储氢量达 2.8 wt%,通过高压 CO₂活化处理,微孔体积从 0.8 cm³/g 增至 1.2 cm³/g,储氢量提升 20%。氨基修饰的 MOF-74 (Zn) 表面的极性位点增强 H₂分子的四极矩相互作用,吸附热从 5 kJ/mol 提升至 8 kJ/mol,实现室温(25℃)、100 bar 下储氢量 1.8 wt%。
4.2.3 有机液体储氢:催化脱氢与载体优化
-
甲基环己烷(MCH)体系:负载于介孔 SiO₂的 Pt-Pd 双金属催化剂(1:1),使 MCH 脱氢温度从 280℃降至 220℃,脱氢速率达 0.8 mol H₂/(mol Pt・h),优于单一 Pt 催化剂(0.5 mol/(mol・h))。载体的介孔结构(孔径 5 nm)抑制金属颗粒团聚,循环 50 次后活性保持率 > 90%。
-
氨硼烷(NH₃BH₃):纳米晶氨硼烷(粒径 < 100 nm)与 LiBH₄形成共晶混合物,储氢容量达 15 wt%,通过添加 NaH(2 wt%)作为脱氢抑制剂,使放氢温度窗口从 60-120℃窄化至 80-100℃,便于燃料电池实时供氢。
五、氢能转换新材料:燃料电池从铂基依赖到无贵金属化的跨越
5.1 阴极氧还原反应(ORR)催化剂:非贵金属替代策略
5.1.1 过渡金属氮化物(M-N-C)
-
Fe-N-C 催化剂:通过高温热解 FePc/Zn-ZIF-8 前驱体,制备出 Fe 单原子与 N 掺杂碳纳米管(CNT)复合催化剂,在 0.1 M HClO₄中半波电位(E1/2)达 0.88 V vs RHE,仅比 Pt/C 低 20 mV,且耐甲醇性能优异(1 M CH₃OH 中电流衰减 < 5%)。XPS 分析显示,Fe-N₄结构占比达 70%,是 ORR 的主要活性位点。
-
双金属协同:Co-Fe-N-C 催化剂的 E1/2 达 0.90 V vs RHE,其性能提升源于 Co²⁺与 Fe³⁺的氧化还原偶合,加速 O₂分子的吸附 - 解离过程,DFT 计算显示 O-O 键断裂能垒从 1.2 eV 降至 0.8 eV。
5.1.2 碳基催化剂:缺陷工程与杂原子掺杂
-
边缘富集型石墨烯:通过氧等离子体刻蚀制备边缘含 N、S 共掺杂的石墨烯纳米片,ORR 起始电位达 0.92 V vs RHE,在碱性电解液中电子转移数接近 4(3.85),其活性源于边缘不饱和碳原子与杂原子的协同效应。
-
金刚石纳米颗粒:表面羟基化的金刚石(100 nm)在酸性条件下展现出优异的 ORR 稳定性,10000 次循环后 E1/2 衰减仅 5 mV,远优于 Pt/C(50 mV),适用于长寿命燃料电池。
5.2 膜电极组件(MEA):界面优化与材料耐久性
5.2.1 质子交换膜(PEM)
-
全氟磺酸膜改性:Nafion 膜中嵌入 0.5 wt% 的 GO-COOH 纳米片,质子传导率从 0.08 S/cm(80℃)提升至 0.12 S/cm,同时吸水率从 25% 降至 15%,减少高温下的溶胀变形。表面接枝的磺酸基团形成离子通道,使膜电阻降低 20%。
-
无氟质子膜:聚苯并咪唑(PBI)膜掺杂 10 wt% 的磷酸(H₃PO₄),在 150℃高温下质子传导率达 0.05 S/cm,无需增湿系统,解决了 Nafion 膜在高温下的脱水失效问题,适用于车载燃料电池。
5.2.2 双极板材料
-
表面改性金属双极板:316L 不锈钢表面镀覆 5 μm 厚的 TiN 涂层,接触电阻从 150 mΩ・cm² 降至 50 mΩ・cm²,在 0.6 V vs SCE 电位下腐蚀电流密度 < 1 μA/cm²,寿命超过 5000 小时,成本较石墨双极板降低 60%。
-
碳纤维增强复合材料:碳纤维(60%)与聚醚醚酮(PEEK)复合双极板,体积电导率 > 100 S/cm,密度 1.8 g/cm³,抗冲击强度达 80 kJ/m²,满足车载燃料电池的振动与轻量化需求。
5.3 阳极氢氧化反应(HOR)催化剂:抗 CO 中毒与稳定性强化
5.3.1 铂基催化剂的抗毒化改性
-
合金化与表面修饰:Pt-Pd-Ni 三元合金催化剂(原子比 5:3:2)在 CO 吸附测试中展现出优异抗性,CO 脱附温度从 200℃提升至 300℃,源于 Ni 原子的电子效应降低 Pt 表面 CO 吸附能(从 - 0.9 eV 降至 - 0.6 eV)。XPS 深度剖析显示,表面 Pd 富集层(厚度 2 nm)有效阻隔 CO 分子与 Pt 活性位点的直接接触,使含 100 ppm CO 的燃料气中性能衰减速率降低 70%。
-
核壳结构设计:Pt@CoO 核壳纳米颗粒的 HOR 质量活性达 2.5 A/mg Pt(@0.9 V vs RHE),是商业 Pt/C(0.8 A/mg Pt)的 3 倍,且 CO 耐受浓度提升至 500 ppm。壳层 CoO 的氧空位缺陷促进 H₂O 吸附,通过 “水煤气变换” 原位清除 CO,实现自修复功能(图 5)。
5.3.2 非贵金属 HOR 催化剂探索
-
过渡金属磷化物:Ni₂P 纳米片在碱性电解液中的 HOR 交换电流密度达 5.2 mA/cm²,较纯 Ni 提升 10 倍,其活性源于 P 原子诱导的 Ni 电子结构重构(d 带中心上移 0.15 eV)。原位 Raman 显示,Ni-P 键在反应中动态调整,形成高活性的 Niδ+-P 界面位点。
-
单原子合金催化剂:Cu 单原子分散在 Pd 纳米颗粒表面(Cu-Pd SAAs),HOR 过电位仅 25 mV(10 mA/cm²),CO 吸附能降至 - 0.5 eV,优于传统 Pd 基催化剂。这种 “单原子隔离效应” 通过抑制 CO 分子的桥式吸附,实现抗毒化性能与活性的协同提升。
5.4 电解质膜材料:从质子传导到多场景适配
5.4.1 高温质子交换膜(HT-PEM)
-
磷酸掺杂聚苯并咪唑(PBI)膜:引入 10 wt% 的 Zr (HPO₄)₂纳米棒作为酸锚定位点,使磷酸保留率从 60%(180℃)提升至 85%,质子传导率在 200℃下稳定维持 0.03 S/cm。该膜应用于高温燃料电池(HT-PEMFC),发电效率达 55%(高于低温 PEMFC 的 45%),且 CO 耐受浓度从 50 ppm 提升至 500 ppm。
-
复合离子液体膜:1 - 乙基 - 3 - 甲基咪唑四氟硼酸盐(EMIM-BF₄)与二氧化硅气凝胶复合膜,在 150℃无增湿条件下质子传导率达 0.04 S/cm,兼具离子液体的高导电性与气凝胶的机械强度,适用于沙漠等干燥环境。
5.4.2 碱性燃料电池(AFC)膜材料
-
季铵化聚醚砜(QPESU)膜:通过侧链引入三甲基铵基团(TMA+),氢氧根传导率达 0.06 S/cm(25℃),阴离子交换容量(IEC)达 1.8 meq/g。膜表面的亲水性改性(接枝 PEG 链)使水吸收速率提升 3 倍,解决了碱性条件下的膜脱水问题。
-
双极膜技术:阴离子交换膜(AEM)与阳离子交换膜(CEM)复合形成的双极膜,可在同一膜内实现 H⁺与 OH⁻的定向迁移,用于水电解器时槽电压降低 0.1 V,能耗从 4.5 kWh/Nm³ 降至 4.2 kWh/Nm³。
六、跨环节协同创新:材料体系的全产业链适配
6.1 制氢 - 储氢耦合材料设计
6.1.1 电解水 - 固态储氢一体化
-
催化 - 储氢双功能材料:Ni-Co 合金纳米颗粒负载的 Mg 基储氢材料,在电解水制氢时作为 HER 催化剂(过电位 100 mV),储氢时通过合金催化 MgH₂脱氢(温度降低 50℃),实现 “制 - 储” 过程的催化剂复用,系统能效提升 15%。
-
热管理材料集成:将相变材料(PCM,如石蜡)与储氢材料复合,利用电解水废热(60-80℃)驱动 MgH₂脱氢,使储氢系统的能量自给率达 70%,解决了传统储氢需要额外供热的问题。
6.2 分离 - 转换环节材料匹配
6.2.1 燃料电池级氢气提纯膜与电极协同
-
膜电极集成设计:将 MOFs 膜直接贴合于燃料电池阴极流道,实时提纯含 5% CO₂的原料氢,膜的 H₂渗透率(1000 Barrer)与电极反应速率(0.5 A/cm²)精准匹配,避免传统外置提纯装置的压降损失(减少 0.3 bar 压降)。
-
杂质响应型膜材料:pH 敏感的聚丙烯酸 / 沸石复合膜,在 CO₂浓度 > 1% 时自动收缩孔径(从 0.4 nm 至 0.3 nm),优先阻断 CO₂渗透,确保燃料电池入口 H₂纯度 > 99.97%,这种智能响应特性使系统维护周期延长至 1000 小时。
七、产业化关键技术:从材料制备到系统集成的工程化挑战
7.1 制氢催化剂的规模化制备
7.1.1 喷雾热解技术
-
连续化生产设备:直径 1.5 米的喷雾热解反应器,处理量达 50 kg/h,制备的 Co-Fe 层状双氢氧化物(LDH)催化剂粒径分布系数(Cv)<5%,较传统共沉淀法(Cv=15%)显著提升均匀性。热解温度精准控制(±2℃)使催化剂活性位点占比从 60% 提升至 85%。
7.1.2 微波辅助合成
-
节能型工艺:微波加热(2.45 GHz)使催化剂合成时间从 12 小时缩短至 1 小时,能耗降低 60%。以 Ni-Mo 硫化物为例,微波法制备的材料比表面积达 200 m²/g,是常规水热法的 2 倍,活性位点暴露量增加 30%。
7.2 储氢材料的工程化改性
7.2.1 表面包覆工业化技术
-
流化床包覆机:采用气固流化床对 MgH₂颗粒进行石墨烯包覆,包覆均匀性达 95% 以上,处理量达 100 kg/h。包覆层厚度可控(5-50 nm),且石墨烯利用率从实验室的 60% 提升至工业级的 85%。
7.2.2 纳米限域技术量产
-
阳极氧化铝(AAO)模板法:通过工业级 AAO 模板(孔径 50 nm,孔隙率 80%)批量制备碳纳米管 / 金属氢化物复合储氢材料,模板重复利用率 > 50 次,单批次产量达 5 kg,为固态储氢罐的规模化生产奠定基础。
7.3 膜材料的卷对卷制造
7.3.1 溶胀 - 拉伸定向技术
-
高分子膜工业化生产线:在 100 米长的卷对卷设备上,通过溶胀 - 拉伸工艺使聚酰亚胺膜的微孔定向排列,H₂渗透率提升 20%,分离系数波动 < 3%。生产线速度达 5 m/min,年产能达 10 万平方米。
7.3.2 MOFs 膜的化学气相沉积(CVD)放大
-
常压 CVD 反应器:直径 300 mm 的流化床 CVD 装置,实现 ZIF-8 膜在陶瓷载体上的均匀生长,膜厚可控(50-500 nm),缺陷密度从 10⁵个 /cm² 降至 10³ 个 /cm²,满足工业级分离装置的高通量需求。
八、政策与标准驱动下的材料研发导向
8.1 国际前沿技术布局
8.1.1 美国 DOE 氢能材料目标
-
2030 目标:制氢催化剂成本 < 20 $/kW(当前Pt基>200 $/kW),储氢材料质量储氢密度 > 7.5 wt%(当前 Type IV 瓶 5.5 wt%),燃料电池寿命 > 8000 小时(当前 < 5000 小时)。
-
关键路径:启动 “材料基因计划” 氢能专项,通过高通量计算筛选 10 万种催化材料,目标将实验室到产业化周期从 10 年缩短至 5 年。
8.1.2 欧盟氢能战略材料路线图
-
重点方向:开发适用于 700℃高温电解槽的陶瓷电解质材料(如掺杂 Ce 的 GDC 膜),目标电解效率 > 90%;推进固态储氢材料标准化,2025 年前建立储放氢循环寿命测试标准(ISO/TS 20108-4)。
8.2 中国 “十四五” 氢能材料攻关重点
8.2.1 “绿氢” 关键材料国产化
-
“卡脖子” 突破:国产燃料电池用碳纸(厚度 190 μm,面电阻 < 10 mΩ・cm²)已进入中试阶段,打破日本东丽的垄断;自主研发的电解水制氢用钛基 IrO₂涂层(厚度 5 μm),寿命达 1500 小时,接近国际先进水平(2000 小时)。
8.2.2 标准化体系建设
-
测试平台布局:建成北京、上海、广东三大氢能材料检测中心,涵盖催化剂活性(旋转圆盘电极测试)、膜材料耐久性(加速老化箱)、储氢材料安全性(绝热温升测试)等 50 余项检测能力,填补国内标准空白。
十、结论:材料创新筑牢氢能产业发展根基
氢能新材料的研发不仅是单一技术的突破,更是涉及材料科学、电化学、工程热物理的交叉学科协同。从制氢环节的非贵金属催化到储氢领域的固态材料,从分离提纯的智能膜材料到转换环节的无铂电极,每个突破都伴随着机理认知的深化与制备技术的革新。未来需强化 “需求定义材料 - 材料驱动系统 - 系统反哺材料” 的闭环创新,结合数字化设计与绿色制造技术,攻克稳定性、成本、规模化生产等核心难题。随着材料性能的持续提升与产业链的成熟,氢能有望在 2050 年承担全球 18% 的能源需求,而新材料将始终是这一进程中最坚实的技术基石。
共有 0 条评论