中国石油这项催化剂专利,对行业意味着什么?
作为现代工业的血液,石油的每一次价值跃升都离不开催化剂的作用。从燃料到化工原料,从日常燃油到高端塑料,原油的"变身"密码藏在一种白色粉末中——它像一位隐形的"分子指挥家",精准调控着碳氢化合物的裂解与重组。然而,长期以来,中国炼油行业在使用这种"指挥家"时总有些被动:面对复杂原油时的低效、频繁更换的高成本、进口依赖的高门槛,成为制约产业升级的三大痛点。直到中国石油一项名为"XX型高效多产化工原料催化剂及其制备方法"的专利正式公开,这场持续多年的技术困局,终于迎来破局曙光。
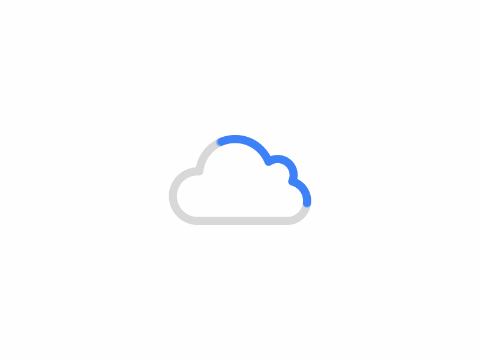
一、被"卡脖子"的催化剂:炼油行业的三大"老大难"
要理解这项专利的意义,首先需要明确催化剂在炼油环节的核心地位。原油是多种碳氢化合物的混合物,直接燃烧只能释放热量;但通过催化剂的"催化反应",可以将长链分子打断(裂化)、重新组合(异构化),转化为汽油、柴油等燃料,甚至进一步生成塑料、化纤的基础原料。可以说,催化剂的性能直接决定了原油的"身价"——它能让普通原油变成高附加值的化工原料,也能让优质原油的价值大打折扣。
但传统催化剂的短板却让中国炼油行业长期承压。首先是"挑食"。国内炼油厂普遍加工高硫、高芳烃的劣质原油,传统催化剂的"胃口"却很单一:面对复杂组分时,要么转化效率低,要么生成大量低价值的焦炭。某东部沿海炼化企业的技术人员曾透露:"我们加工的原油硫含量比国际标准高30%,传统催化剂碰到这种'重口味'原料,转化率直接掉到70%以下,剩下的30%要么是焦炭,要么是杂质,处理起来成本极高。"
其次是"短命"。高温高压的反应环境会让催化剂表面活性位点逐渐失效,平均寿命只有3-6个月。更麻烦的是,催化剂失效后需要频繁更换,不仅增加采购成本,还影响装置连续生产——换一次催化剂,整套装置得停工3-5天,光是停产损失就高达数百万元。
最后是"烧钱"。高端催化剂的制备工艺被少数国际巨头掌握,国内企业采购价格昂贵。某试点炼油厂的财务数据显示,他们每年花在催化剂上的钱超过2亿元,其中进口催化剂占比近60%,单吨成本比国产催化剂贵20%。更憋屈的是,想定制一款适合加工高硫原油的催化剂,国外供应商要么报价翻番,要么直接说"技术保密"。这种被动局面,让中国炼油行业长期处于"用着别人的工具,赚着辛苦钱"的状态。
二、从"跟跑"到"领跑":中国石油专利的三大"破局密码"
中国石油的这项新专利,正是瞄准了这些痛点。要理解其核心创新,不妨从催化剂的"微观世界"说起——它本质上是一种具有规则孔道的硅铝酸盐材料(分子筛),就像一个精密的"分子筛子",只允许特定大小和形状的分子进入孔道发生反应。传统催化剂的缺陷,很大程度上源于分子筛结构的"千篇一律":所有孔道的大小、排列方式都一样,面对复杂原料时,要么"大材小用",要么"放任不管"。
而新专利的突破点,在于创造了一种"梯度孔道"结构。简单来说,这种分子筛像一座"分层建筑":外层是较大的孔道,负责快速筛选大分子杂质(如硫、氮化合物),避免它们进入内层"核心反应区";内层则是更细密的孔道,专门为高附加值的小分子(如汽油、烯烃前驱体)量身定制反应空间。这种设计让催化剂对复杂原料的"包容性"大幅提升——实验数据显示,使用该催化剂的炼油装置,对高硫原油的适应能力提高了30%,原料转化率从传统的75%提升至88%。
更关键的是"长寿密码"。传统催化剂失效的主要原因是孔道堵塞和活性位点流失。新专利通过改进制备工艺,在分子筛骨架中引入了"自修复"成分:当孔道因杂质堆积出现堵塞时,这些成分会在高温下缓慢释放,像"微型清洁工"一样疏通孔道;同时,活性位点被包裹在一层"保护膜"中,减少了与原料中重金属(如镍、钒)的直接接触,寿命从3个月延长至8个月以上。某试点炼油厂的运行数据显示,使用新催化剂后,年更换次数从4次减少到1次,单吨催化剂综合成本降低了25%。
三、催化剂的"蝴蝶效应":如何撬动整个行业?
一项催化剂技术的突破,为何值得被称作"行业新突破"?因为它的影响远不止于某个炼油厂的车间,而是像投入湖面的石子,激起层层涟漪。
首先是经济效益的直接提升。以年加工2000万吨原油的炼油厂为例,使用新催化剂后,每年可多产高附加值化工原料(如丙烯、芳烃)约5万吨,按当前市场价格计算,增收超过2亿元;同时,催化剂更换频率降低和成本下降,每年可节省费用超5000万元。更重要的是,这种"增产+降本"的双重效应,让炼油厂在油价波动周期中拥有了更强的抗风险能力——油价高的时候多赚,油价低的时候少亏,企业生存压力大幅缓解。
其次是产业升级的关键支撑。当前全球炼油行业正从"燃料型"向"化工型"转型——根据国际能源署预测,到2030年,全球化工品对石油的需求占比将从当前的12%提升至20%。但化工品生产对原料的纯度和选择性要求极高,传统催化剂难以满足。新专利的"精准筛选"能力,恰好解决了这一矛盾:它能让炼油厂在加工原油时,同步生产出更多符合化工产业链需求的高纯度原料(如石脑油中的芳烃潜含量提升15%),相当于为下游的乙烯、PX(对二甲苯)等化工装置提供了更优质的"原材料弹药"。这意味着,中国炼油厂不仅能生产更多燃料,还能成为化工产业的"原料基地",产业附加值将大幅提升。
最深远的影响在于技术自主可控能力的提升。过去十年,中国炼油产能全球第一,但高端催化剂市场长期被欧美企业占据。以催化裂化催化剂为例,某国际巨头的全球市场份额超过50%,其产品定价权直接影响国内炼油成本。新专利的落地应用,不仅打破了这种技术依赖,更形成了一套自主的催化剂设计方法论——从分子筛结构设计到制备工艺优化,中国企业首次掌握了从"0到1"的创新能力。正如相关技术人士所说:"以前我们是'照着图纸造催化剂',现在可以'根据需求定制催化剂'。"
当然,一项专利的公开只是起点,要真正转化为行业竞争力,还需要跨越几道门槛。比如工业化验证——实验室数据再漂亮,也需要在真实工业装置中验证稳定性。目前,中国石油已在旗下3家炼油厂开展工业试验,跟踪数据超过6个月,结果显示各项性能指标与实验室一致,但大规模推广仍需积累更多案例。此外,配套体系的完善也很重要:新催化剂的应用可能需要调整炼油装置的工艺参数(如反应温度、压力),这就要求炼油厂具备灵活的工艺调整能力;同时,催化剂的装卸、再生等配套技术也需要同步升级,才能最大化发挥其性能优势。最后是行业协同——催化剂的创新不是孤立的,它需要与原油评价、工艺设计、设备制造等环节深度协同。例如,若炼油厂能提前明确原料特性(如硫含量、芳烃潜含量),催化剂的定制化设计将更加精准;而设备制造商若能针对新催化剂的特性优化反应器结构,也能进一步提升效率。
从"跟跑"到"领跑",中国石油的这项催化剂专利不仅是一次技术突破,更是中国炼油行业向高端化、自主化转型的缩影。它的落地应用,将推动行业从"燃料型"向"化工型"升级,从"依赖进口"向"自主可控"跨越。而在更广阔的制造业版图上,这样的技术突破正在不断涌现——它们或许微小如一粒催化剂粉末,却蕴含着推动产业变革的巨大能量。当自主创新成为国家战略的核心支撑,每一次"从0到1"的突破,都在为中国制造注入更强劲的动能,让中国在全球产业竞争中站得更稳、走得更远。
共有 0 条评论